By: Steve Haralampu, Sc.D. & Bill Skea, Ph.D.
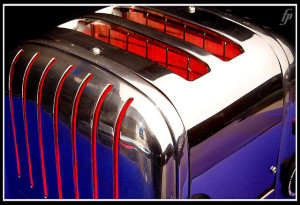
Every technology company strives to offer the best thing since sliced bread. Achieve commercial excellence with these key insights.
Successful commercialization of a new technology has more to do with marketplace needs and product execution than with the technology itself. The main factor driving success is the customers’ perception of value: “What does it do for me?” and “Is it better, faster, or cheaper?” Technology rarely sells for technology’s sake. We will discuss some factors to consider during the commercialization process. Although the concepts are generally applicable to all product development efforts, we concentrate on how these relate to the introduction of new tools for life science R&D and diagnostics laboratories, especially within startup companies or other small organizations.
Changing Priorities: Transitioning from Bench to Product Development
Product development and commercialization is a truly multidisciplinary activity, especially at the beginning of the process: the product specification. The focus should be on filling customer needs. Traditionally, sales and marketing is the conduit to the marketplace, and they should be involved in defining what the customer wants, but too frequently they are the sole drivers. Scientists that develop novel technologies have unique insights into their potential for being revolutionary, and to see outside of the conventional box. How a product is specified and developed also depends upon design and manufacturing constraints. The main design constraints are product complexity, such as automation, which drives product cost and time to market; and design for manufacture and assembly (DFM/DFA), which also drives cost, and whether a product can be made or repaired. Finally, the whole process is driven with money. Finance must be at the table to assure that the product development and commercialization effort is affordable. A product funded for 95% of its commercialization is still not a product. Resources must be available to cross the finish line. Therefore, an agile team of scientists, engineers, marketers and financers, each with the ability to wear many hats, and each with roughly equal input, drives a successful product commercialization effort, since each has a stake in the outcome. Since the product development effort is usually a period of intense activity, and is an activity with which a small organization is not constantly involved, it makes sense to share some of the workload with external resources. Otherwise, at the end of the process, an organization can be stuck with excess headcount.
A major consideration in the specification and design of a product is developing a strategy for how it will be manufactured and distributed. Manufacturing entails investment in manufacturing space, equipment, and personnel. This investment can be significant, and can be the burden that breaks an organization if product rollout is late, or sales do not meet projections. There are many vendors that provide contract-manufacturing services. Whether it is the whole product, product subsystems, or final assembly and packaging, the use of contract-manufacturers can significantly reduce financial risk in the early stages of a product’s life cycle. Determining how vendors play into the overall manufacturing scheme can impact product design. It can be extremely valuable to give your contract-manufacturing vendor a seat at the table during product development, to assure a design for manufacture, and to avoid surprises late in the game.
Associated with early-stage manufacture is a realistic sales projection, or a willingness to manufacture to orders. Excess inventory of an expensive laboratory instrument ties up huge amounts of capital needed for an organization’s growth. Maintaining financial flexibility during product rollout is important should it be necessary to redirect efforts into sales or applications development.
Six insights to keep you on the path to success
All of this is common sense, and most managers feel like they would never fall into any traps posed by the product development and commercialization process. This does not seem to be the case, however, since there are so many examples of organizations that stumble, sometimes fatally. Heeding the admonition, “Those who cannot remember the past are condemned to repeat it.” we give some real examples from which we can learn.
- Technology Evaluation/Due Diligence Alone Is Not Enough
Even before a technology is approved for product development, before a startup is approved for funding, or during due diligence of an acquisition target, the projected product development process needs to be evaluated. Sometimes inventors are so close to the technology that they do not recognize the marketplace landscape they are trying to enter. This can be particularly true, for example, when a technology is developed by physicists and/or engineers and is to be applied to diagnostics. It is typically not within their realm of experience to understand the technology alternatives or regulatory landscape.
A clear sign of being too focused on the core technology is making the statement, “We have no competition.” A core technology may be so revolutionary that there is indeed no competition that performs its specific task. What can be unrecognized is that there are perfectly adequate alternative technologies for performing the task. One team of inventors developed a methodology for detecting metabolic stresses within living cells. Another established company had a similar physical product already on the market. When the team was asked how they were better than this competition, their response was, “They’re not competition because they measure amplitude modulation, our invention measures frequency modulation.” One needs to have very solid intellectual property protection if one plans to enter a marketplace and not expect competition when the method of data analysis is the only point of differentiation. The technology is good, but the inventors did not adequately evaluate its potential versus competitive stresses.
- Listen to the Customer (sometimes)
It is important for a product to be successful that it fulfills some unmet need of the customer. Although this is true, end users do not always recognize their unmet needs, especially with regard to technologies that require a paradigm shift. Therefore, asking sales and marketing to poll customers for their needs, tends to generate feedback that is incremental improvement of known product forms. Apple, Inc. has been a leader in creating marketplace needs for its new products.
With respect to laboratory products, it is important to understand the customers’ workflow. A product might do amazing things, but if it does it in a way that is not helpful, it will not be a success. One company had an interesting platform for growing cells. Their development team designed a product that compared a control to a test under a wide variety of environmental conditions. This seemed logical to the design team. However, research is normally done using plates with 24 or 96 wells, not just 2. The company had a good idea, but its execution did not meet the most common workflow.
Small organizations tend to focus on the new technology. A lot of this is driven by the fact that completion of the technology development is going on concurrently with the early stages of product development, and, after all, new technology perfection is what the small organization is all about. One company developed a technology to separate proteins in a way that enhanced the research information obtainable once the proteins were further analyzed. Unfortunately, that company did not provide the customer with an adequate way to retrieve the separated proteins from its product and into the downstream analyses. Although the technology met customer needs, the overall product system execution was not useful in the laboratory workflow.
- Customers Don’t Like to Read Instructions
Once a technology is demonstrated and shown to be useful, the technology development must focus on making that technology execution robust. An inadequate technology execution is when: failure rates are high, and it takes a skilled practitioner in the technology to recognize the failures, but when it works, it’s great! Technology developers need to realize that they probably have an extraordinary skill at getting things to work, while the customer may not be willing to invest this kind of time to come up on the learning curve. Technology developers deal with the technology 100% of the time, customers deal with most technologies only a fraction of the time as part of a larger workflow. Therefore, they cannot focus on the nuances of running a finicky product. A technology needs to be simple (sometimes requiring significant automation to conduct the difficult tasks) and needs to work reproducibly and flawlessly. One company’s product was based on an array of test sites. Each test site had >99% reliability, but since there were 41 test sites on the product, and each needed to work for the product to have worked, there was only a 65-70% chance that the product worked. This was unacceptable in most laboratory situations.
- Beware: The Misguided Cost Estimate
Especially with regard to the micro- and nanotechnologies being developed today, product cost estimates that drive the business plan can be based on faulty/excessively optimistic assumptions. One company developed a rather extraordinary biochemical sensor that was based on a silicon chip only 0.2 x 0.2 mm. The materials cost for the sensor was only cents. Micro- and nano-scale products use very little material because of their size. The fault in the analysis was that the nanosensor still needed to interface with a macro world. The product cannot be a box of grain-of-sand-sized sensors. A housing to allow a customer to handle the sensor, along with the appropriate plumbing to get the sample prepared and to the sensor cost as much as an alternative sensor technology for the base application they chose. The core technology probably still has great potential, but an application needs to be found where its small size is the advantage, and enables sensing in places unattainable by the alternative technology.
- Product Design is a Predictable Task, or is it?
Many aspects of product design are predictable. It is merely the engineering task of finding OEM components or designing custom parts and fitting these together in an operable system. What could go wrong? Missing cost targets, inappropriately setting priorities, or inadequately integrating systems are frequent issues.
Engineering design is fun for those involved, but sometimes it is hard to know when to stop. Over design with too many features can make a product too expensive, and/or unreliable. Some features are just annoying. One company decided to have its product send a stream of text messages to the operator’s cell phone updating the instrument’s status. This sounded novel and useful, but in practice was just annoying. That same company decided to custom design most of its mechanical components. This approach was in some cases expensive, but more importantly did not leverage the knowledge base of OEM suppliers. Consequently, some components did not perform as expected, which ate up valuable development resources to debug components that could have been purchased with proven performance. Too much time was spent resolving issues that could have been purchased, and defocused the team from its core technology and applications development. This company failed.
We are accustomed to seeing sculpted cases used in consumer products around us. It is an attractive concept to create products with an eye-popping “look”. This is possible for products manufactured by the thousands, but sculpted skins for products manufactured by the hundreds can be surprisingly expensive. This is an example of an inappropriate priority in a resource-limited environment, and where paint might be a better alternative.
The product design effort is not complete with a final set of product blueprints. There is still substantial work to be done producing support materials. The user manual is not just a set of step-by-step instructions for the customer, but is also a legal document that is used to support safety testing and certification. It has a particular format and set of regulatory requirements. Another neglected aspect of product design completion is product packaging. One company had great success beta testing its product at the university located across the street from their headquarters. The same could not be said for beta tests at major research centers halfway across the country. Placing the instrument in a shipping crate was not sufficient protection. Beta testers received product, with screws missing (loose in the shipping container) and critical components out of alignment. Needless to say, these beta testers were never converted to customers.
- Transitioning from Prototype to Manufactured Product
The main pressure of an organization is to get income as early as possible, and to manage cash flow. This drives some compressed schedules, and encourages cutting some corners. Sending a product design to manufacturing too early can have profound consequences. When a design flaw is detected in the design phase, it may be expensive to fix, but it is preferable to fix it before the flaw is replicated by the manufacturing process. Just think about the costs associated with retrofitting multiple products in inventory, or in the field in comparison with taking the time to assure the design to manufacturing is correct.
Inevitably, some flaws in product design go undetected until the product is stressed in the marketplace. One company did not make it that far. They experienced too many bumps in the road during product development, so they were running out of money. The product still had severe flaws. They decided to launch the flawed product because investors promised that they would provide more capital if the company demonstrated they could sell product by the end of the quarter. The company’s management thought that selling flawed products would buy them enough time to fix the product later. Unfortunately, customers were not willing to pay full price for a product that virtually did not work. No products were ever sold.
Two clichés come to mind:
- You only have one chance to make a first impression.
- If we don’t have enough time to do it right, why do we have enough time to do it twice.
In Conclusion
Nearly every function within a company has a vested interest in the success of product commercialization. The commercial product is the physical manifestation of years of work, and is what will bring reward to the development team. The product development task requires teamwork between corporate functions that typically do not have much interaction. Lack of appreciation of the constraints of a given function by team members leads to disaster, e.g., specifications/expectations that cannot be met by the technology or by the design team; specifications that cannot be supported by finance; designs that are difficult to manufacture; executions customers do not want; etc. The commercialization process is capital intensive, and has very little leeway for errors. Product commercialization uses unique skills and experience not needed 100% of the time within an organization. Outsourcing is a great option to minimize risks during this critical growth function.
Picture Credit: fensterbme via photopin cc